Industrial inkjet printing technology has been widely adopted in various business sectors as the application of choice because of its manufacturing flexibility, variable information capability, quick turnaround times, cost effective shorter runs, energy reduction and potential materials savings.
In the automotive sector, key drivers for evaluating inkjet for the application of hard coats include the reduction of waste and more efficient manufacturing.
Inkjet can provide precise positioning with almost no overspray, enabling the coating of complex parts without the need for masking. The digital control of drops means that selective coating and texturing is also possible.
Global Inkjet Systems (GIS) has been working with Momentive fluids and has proven inkjetting of their SilFort range of automotive approved hard coats. These hard coats can be used to prolong the long-term durability and performance of plastics such as polycarbonate and PMMA for interior automotive parts, or to resist abrasion from chemicals and solvents to maintain colour, gloss, or anti-glare attributes on external elements.
Inkjet has also started to be used for colour decoration of interior (and some exterior) components enabling short runs of special editions and even personalisation of automotive parts.
Advanced software for direct to shape
With extensive expertise in the development of advanced drive electronics, software and fluid delivery systems for leading inkjet brands, GIS has developed Atlas® Direct-to-Shape (DTS) Studio software, specifically created to enable the efficient and accurate use of inkjet to apply full or selective coverage of protective hard coatings or graphics to complex shapes. This proprietary software suite incorporates tools such as Print Path Designer and Digital Mask Editor, plus drivers to export print and transport data to the inkjet printhead and robotic handling system.
GIS Print Path Designer generates print paths on complex shapes by placing a series of points across the surface, guided by an interactive display of the area which will be coated or printed. These points are joined to form a path and given a flying height across the shape. Digital Mask Editor is designed to specify masking to specific areas of the shape for selective coverage, while protecting areas that must not be coated. When the path is complete, the system generates instructions for the inkjet process.
Atlas® DTS Studio can be implemented in different system configurations – the component or the printhead can be mounted onto the robot arm – so that there is no limitation on the size of component.
In complex shape printing, stitching is a key area where inaccuracies will show, and positioning errors cause gaps or overlaps. Therefore, careful control is required to manage transport accuracy, print synchronisation, and target shape variations from nominal dimensions.
In summary, the challenges presented by fluids and printhead capability may still be present but advances in software are paving the way for numerous opportunities to accurately inkjet print and coat complex automotive components, improve production efficiencies and time to market, and provide additional customisation benefits.
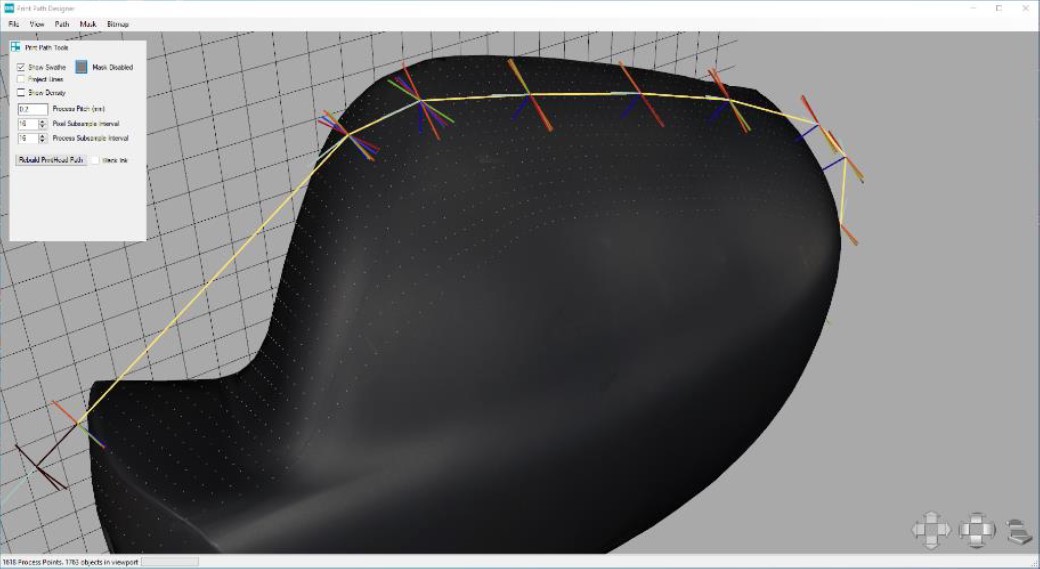
Print Path Designer
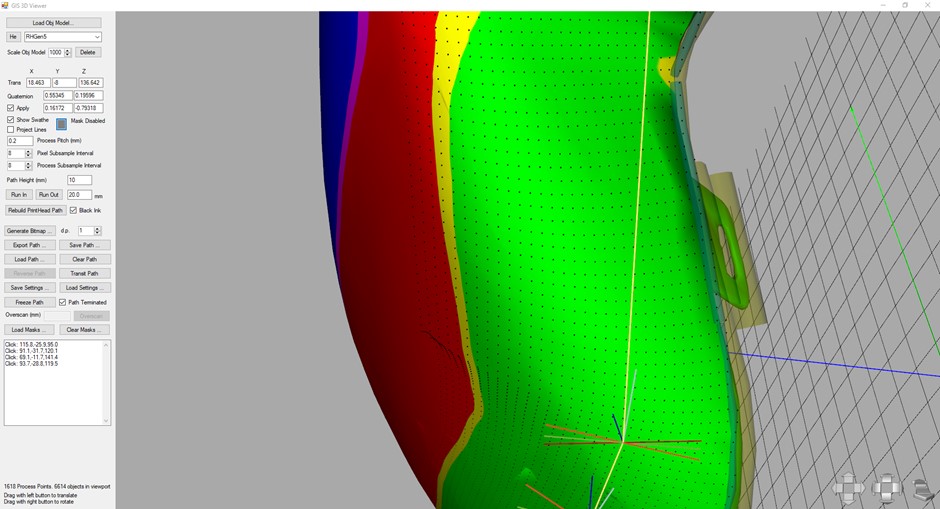
Digital Mask Editor