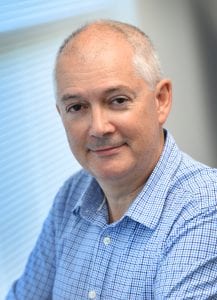
Phil Collins – Director – Advanced R&D
Digital printing has come a long way since its inception and use for flat surfaces. Although flat substrates still make up the majority of digital printing applications, we are seeing an increase in inkjet’s use to directly image onto finished products in a wide range of sectors. In fact, it is being seen in both printing and coating applications where either a process step can be removed, such as a label, or reducing over-spray when applying a protective coating to parts. Printing onto complex shapes opens a host of new challenges that were never seen before in traditional printing. We asked our own Phil Collins (Director – Advanced R&D) to tell us the 5 key considerations that need to be taken into account when developing a direct-to-shape inkjet printing solution.
1. The Shape of the Product
Product shape is an important consideration for inkjet printing and can impact the time taken to complete the process. Traditional flat substrates can now be printed at high speed, but the more complex the shape, the more complicated it is to coat or print, which affects throughput. Products that have a small radius of curvature require extra movement of the transport system to ensure that the surface remains the optimum distance from the printhead. So, the process speed versus the advantages of using inkjet are evaluated for each shape and business case.
2. The Choice of Fluid and Printhead
The compatibility of the printhead and fluid is, as always, the first consideration, but with direct-to-shape printing a key factor is also the throw distance required. The physical nature of the fluid as well as the printhead’s available waveforms to enable longer throw distances are critical to direct-to-shape applications. Many direct-to-shape applications are likely to be printed onto non-porous materials, so how the fluid interacts with the surface is important. Knowing this will allow you to decide whether curing can be done once the coating has been completed, or whether low-level pinning might be required.
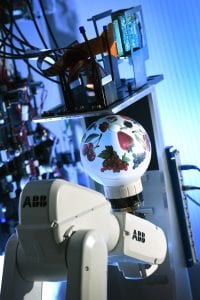
Robotic product transportation
3. The Choice of Transport
In most applications it is likely that the product will be moved, and the printhead remains stationary. For coating a simple moulded product such as e.g. window frames this may be a linear track, but for more complex shapes, robotics are likely to be the only answer. There are many 6-axis robots available off- the-shelf that are flexible enough to present the product to the printhead, but accuracy may be an issue. In these cases, custom mechatronics may need to be developed.
4. Variations in the Size and Shape of the Product
One of the reasons for using inkjet to coat complex shapes is to remove the over-spray often experienced in traditional spray coating methods. The precise nature of inkjet drop-on-demand coating means that it is possible to apply coatings only where they are needed and so avoid this overspray wastage. However, this precision does mean that the process is affected when there are changes in product shape and tolerances. Although production tolerances may be good enough to ensure that the part fits, if these tolerances are too large then there is the risk of errors in stitching, some overspray or the part not fully being coated.
5. Production Throughput
As previously mentioned, the complexity of the product being coated can potentially have an impact on the production throughput. For example, product design changes mean parts could be coated faster, and increasing the number of coating stations would allow more parts to be coated per hour. Optimising the coating, especially on complex shapes, can dramatically improve the cycle time per unit, but this will be dependent upon product shape and the material being deposited.
Benefiting from our Experience
Finding the right partner who has experience in coating and decorating complex shapes can give you the technical advantage to move your project forward. GIS has been working with customers on direct-to-shape applications in a wide range of sectors. These include glass bottles, plastic and metal tubes, pots and tubs for the personal care and food sectors, and now more complex shapes for the automotive industry. Our direct-to-shape experience is also relevant to in-mould label (IML) and in-mould decoration (IMD) applications. With this industry knowledge and experience, your direct-to-shape project could become a reality sooner by speaking with us.